A Blister machine is used to pack the Tablets and capsules by using packaging materials to unit and protect the products from the external environment. Design Qualification (DQ) blister machine including the following contents:
- Objective
- Scope
- Responsibility (Client and manufacturer)
- URS (User Requirement Specification)
- Machine description
- Technical specification
- Brief process description
- Technical specifications of the sub-components/bought-out items, and their make, model & quantity, and backup records/ brochures
- Details of Utilities
- Identification of components for calibration
- Material of construction of all components
- P & ID diagrams for reference & approval
- Equipment orientation with room layout
- Safety features and alarms
- FAT procedure
- Change control procedure
- Design qualification report approval
- Appendix
- Reference Documents
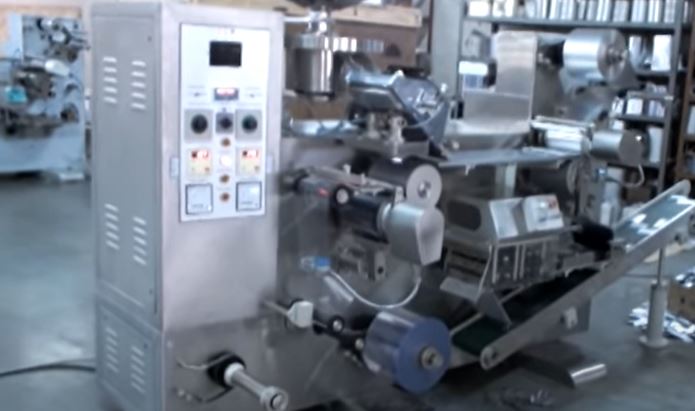
Details of Design Qualification (DQ) Blister machine
1.0 OBJECTIVE:
- To design, engineer, and supply the Blister Packing M/c-Rotovac-210V as per cGMP and cGEP guidelines and to provide assurance that the machine is manufactured as per the URS and complies with the Scope of Supply.
- must demonstrate that every process follows the design specification and that the tolerances set out in the document are the same and completely transparent. The validation process is designed to fully satisfy the client and instill trust in the machine in the user.
2.0 SCOPE:
- The scope of this qualification document is limited to the Design Qualification of Blister Packing M/c-Rotovac 210V.
- This qualification document is a component of the Blister Packing M/c-Rotovac-210V validation activity.
- This qualification document does not cover the qualifying of support utilities.
- The equipment shall be used for pharmaceutical products mainly for packing tablets, drugs, and capsules in blister packs, The equipment shall operate in a dust-free environment and under conditions as per the GMP requirements.
3.0 RESPONSIBILITIES:
CLIENT:
- To provide the URS for the equipment.
- To perform the Factory Acceptance Test (FAT).
MANUFACTURER:
- To design, engineer, and provide the complete technical details of the equipment about its design qualification viz.
(i) Machine overview,
(ii) P&ID drawing,
(iii) Equipment orientation with layout,
(iv) Specifications of the sub-components/bought-out items, and their make, model & quantity, and backup records/brochures,
(v) Details of Utilities,
(vi) Identification of components for calibration
(vii) Material of construction of all components
(viii) Brief process description – details enclosed
(ix) Safety features and alarms
(x) Pre-installation requirements – Refer user’s manual - to assist the client in setting up the machine’s Factory Acceptance Test at their workplace or location.
- To verify that the equipment was delivered to the user site safely.
- To guarantee that no unapproved and/or undocumented design changes will occur. Any time a change to the mutually agreed-upon design is desired, the change control procedure must be followed and documented.
- To make certain that the equipment is installed properly and is properly functional.
5.0 MACHINE DESCRIPTION
The purpose of Design Qualification (DQ) blister machine M/c-Rotovac-210V for packing tablets, drugs, and capsules in blister packs
6.0 TECHNICAL SPECIFICATIONS for Design Qualification (DQ) blister machine
- Name – Blister Packing M/c-Rotovac-210V
- Capacity- 300 Blisters/min
- Model no.- Rotovac-210V
- Base Film Width (Max): 210 mm
- Aluminum Foil Width (Max): 206 mm
- Base Film Thickness: 0.25 mm
- Aluminum Foil Thickness: 0.02 mm
- Useful Forming Area (Max): 210 x 102 mm
- Forming Depth (Max): 10 mm
- Packing Speed of the Tab (Æ 10mm) Max: 2100Packing Speed of the Cap (Size-0) Max: 1600
- Blister Pack Length (Max): 200
- Blister Pack Width: 100
- Machine Cutting Speed ( Max): 150
- Machine Speed during Forming (Max): 4.5 Meters. / Minute.
- External Diameter of PVC Reel: 440 mm
- External Diameter of Al Reel: 210 mm
- Diameter of Reel Core: 70 ~ 76 mm
- Average Power Consumption: 7.5 KVA
- Air Pressure Requirement: 540 Nl /Min at 8Kg/Sq. Cm.
- Input Power Supply: 440 VAC (3PH+N+Gr.)
- Frequency: 50 Hz.
- Cooling Water Flow Rate: 2 Lit / Min at 15~20°c
- ALWAYS USE DEMINERALIZED OR DISTILLED WATER ONLY
- Voltage Stabilizer :
- Type: Servo Controlled
- Input: 316 ~ 500 Volts
- Output : 415 + 1%
- Capacity: 10 KVA
7.0 BRIEF PROCESS DESCRIPTION
Brief Process Description for Design Qualification (DQ) blister machine follows:
Base Material Reel Holder:
- The Base Material Reel Is Loaded On This Unit.
- It Is Used To Support The Base Material During Operation.
- Loading Has To Be Done Manually Onto The Shaft.
- Centering Of The Reel Is Done Manually By Adjusting The Cone On Both Sides Of The Shaft.
- For Centering The Base Material Formula Applicable Is (a/2+151). Here “a” Is The Width Of the Base Material And 151 Is The Machining Center.
- Base Material Detection
- This Assembly Consists Of A Micro Switch, Which Detects The Presence Of The Film Passing Under It.
- If The Film Is Over During The Machine Run, This Switch Would Stop The Machine.
- Alarm / Message: Base Material Finished
Pre-Heating Roller Assembly :
- This Roller Is Used To Preheat The Film Like Pvc, Pvc/PVDC.
- A Pt-100 (RTD) Sensor Is Used To Control The Temperature.
- The “emergency Stop” Switch On the Panel Engages And Disengages The preheating roller And The Blister blister-forming roller.
- During Setting The Pre-heating Roller Should Be Placed 10~15mm Up On The Blister-forming Roller In Disengage Condition When Engaged, It Should Make Perfect Contact With Blister Forming Roller.
Critical:
- Temperature Setting Depends On The Type Of Base Material In Use.
- The Pre-heating Roller May Require Coating On The Surface Depending On The Base Materials.
- Thermo Forming Assembly
- Thermo Forming Assembly Consists Of the BFR Spindle, Coolant Union Housing, And The Vacuum Slip Ring.
- BFR Spindle Is Used To Mount The Blister Forming Roller.
- Coolant Union Housing Contains The Oil Seals Inside The Housing. The Cooling Water Supply Is Connected To The Housing, Which Allows The Water To Circulate In The Blister-forming Roller.
- A vacuum Slip Ring Is a Perfectly Grinded Ring Having Two Chambers Top And Bottom For The Connection Of the Vacuum Line From the Vacuum Pump.
- Blister Forming Roller When Mounted, Its Die Ring Makes The Perfect Contact With The Vacuum Slip Ring To Avoid The Vacuum Leakage.
Blister Forming Roller Assembly
- The Blister Forming Roller Is Used To Form Base Materials Like Pvc, Pvc / PVDC.
- The Blister-forming Roller Assembly Is Mechanically Driven.
- It Consists Of A Blister-forming Roller (change Part) Having A Cooling Chamber, a Vacuum Chamber, And a Die Ring.
- A cooling Chamber Is Used To Cool The Blister Forming Roller To Avoid Excessive Heating Of The Blister blister-forming roller In Contact With the preheating roller.
- During A Machine Running, When The Pre-heated Film Passes Through The Blister-forming Roller, The Perfect Contact Between The Vacuum Slip Ring And The Die Ring Allows it To Form The Blister Exactly The Shape Given On The Blister Forming Roller.
- This Operation Is Continuous.
Critical:
- Temperature Blister Forming Roller To Be Water Chilled At A Temperature Of 18 To 20 Deg. C.
- Vacuum Approx. 24 ~ 28 Inches (depending Upon The Sea Level On The Site Of The Machine)
- Web Tensioner
- The Assembly Web Tensioner Is Located At The End Of The Extension Box Attached To The Main Machine Frame.
- Web Tensioner Assembly Having 3 Guide Rollers, Which Can Be Adjusted In Either Direction Depending Upon The Pack Layout.
- Web Tensioner Assembly Can Be Slid Horizontally To Match The Pitch Of Blisters From Blister blister-forming roller To Counter counter-sealing roller.
Read Also: Multimill Design Qualifications in Pharma
Assembly Bulk Feeder (vibrator):
- Assembly Bulk Feeder Contains The Following Parts:
- Hopper With Lid
- Plain Bowl Dish
- Vibrator
- Vibrator Mounting Assembly
- The Product To Be Run On The Machine Is First Loaded Onto The Hopper On The Machine.
- The Product Then Travels Onto The Bowl Dish Mounted On The Rotary Vibrator.
- The vibrator Is Mounted On The Vibrator Mounting Assembly. The Vibrator Drive Card Is Located Inside The Control Panel that Drives The Vibrator. The Speed Of Vibration Can Be Regulated By A Potentiometer Mounted On The Control Panel Facia Plate.
- On The Top Of The Vibrator, a Plain Bowl Dish Is Mounted. The Product, Which Is Being Transferred From the Hopper To the Bowl Dish, Is Circulated In a Clockwise Direction On Bowl Dish And Finally Transferred To Include a Tablet Feeder Assembly.
- To Avoid The Packing And Spreading Of Excess Powder On The Blister Web The Dust Collection Tray Is Fitted For The Collection Of Powder From the Bowl Dish.
Critical:
- Speed Of Vibrator To Avoid Starvation During Feeding At Rated Speed.
Assembly-inclined Feeder
- The Inclined Feeder Is Used For Feeding Of Tablets, Hard Gelatin Capsules, Oblong Tablets Etc…..
- The Product Enters The Inclined Feeder Box, From The Rotary Bowl Dish Fitted On The Rotary Vibrator.
- The Product Then Slides Down The Inclined Feeding Channel (change Part) Which Is Designed As Per The Product Size Of The Customer And Documented In The Blister Pack Layout.
- The Chevron Roller Is Driven By A Single-phase Ac Geared Motor And Rotates In The Clockwise Direction.
- The Speed Of This Motor Is Variable Depending On The Size And Shape Of The Product And Can Be Adjusted By The Potentiometer Located On The Front Face Of The Machine.
- The Paddle Chevron Roller Is Made Of Food-grade Rubber.
- Depending Upon The Product Thickness The Height Of The Chevron Roller Can Be Adjusted W.r.t. The Inclined Feeding Channel.
- A Photoelectric Sensor Has Been Provided In The Inclined Feeder Box To Control The Quantity Of Products In The Box.
- The Inclined Feeding Unit Has The Provision To Be Adjusted In Left the Right Direction And Angle Adjustment Inclined Feeding Channel Concerning The Guide Track For Smooth Feeding.
Critical: Speed Of The Chevron Roller
- Too High-Speed Will Break The Product And Also Generate Excessive Dust.
- The minimum Hardness Of the Tablet Must Be 4 To 5 Kg.
- If The Hardness Of The Tablet Is Below The Specified Hardness Then The Product May Break In The Chevron Roller
Counter Sealing Assembly
- The Counter Sealing Roller Is Used To Seal Blister-formed Pvc, Pvc / Pvdc Web With The Lidding Material Like Alu. Foil Or Glassine Paper.
- The Counter Sealing Assembly Is Mechanically Driven.
- Counter Sealing Roller (part Of the Change Part) Is Mounted On The Csr Mounting Shaft And Fastened By The Hexagonal Knob.
- Cooling Air Pipe Is Fitted Near The Counter Sealing Assembly To Keep The Counter Sealing Roller Cooled.
- During A Machine Running, The Blister-formed Web Passes Over The Counter Sealing Roller and Gets Sealed With Lidding Material.
- This Operation Is Continuous.
Critical:
- The temperature of the Counter Sealing Roller Should Not Exceed 40~50 Deg. c. To Avoid The Smudging of Blister Web.
Pressure Sealing Roller Assembly:
- This Roller Is Used For Sealing The Lidding Material Alu Foil or Glassine Paper (having Vmch Coating)
- With The Blister Formed Web.
- A Pt-100 (RTD) Sensor Is Used To Control The Temperature.
- The Pressure Sealing Roller Is Engaged With The Counter Sealing Roller While The Machine Is Running In ‘Run’ Mode.
- During Setting The Pressure Sealing Roller Should Be Placed 5~7 Mm Up On The Counter Sealing Roller
- In Disengage Condition And When Engaged It Should Make Perfect Contact With Counter Sealing Roller.
Critical:
- Temperature Setting Depends On The Type Of Lidding Material And Vmch Coating. (normally The Temp. Should Be 180 ~ 200 Deg.c.)
- Sealing Air Pressure Required For Proper Sealing Should Be Min. 6 Bar
- Lidding Material Reel Holder
- The Lidding Material Reel Holder Supports The Lidding Material Reel.
- The Reel Outer Diameter Should Be Max. 250mm And The Core Should Be A Maximum Of 70 To 76mm.
- Loading Has To Be Done Manually Onto The Shaft.
- Centering Of The Reel Is Done Manually By Adjusting The Cone On Both Sides Of The Shaft.
- For Centering The Base Material Formula Applicable Is (a/2+151). Here “a” Is The Width Of The Base Material And 151 Is The Machine Center.
- Critical: Reel Unwinds Direction To Be Maintained.
- Reel Winding To Be Proper And Uniform.
- A damaged Cone Will Cause Improper Fitment Onto The Shaft
- Alarm: End Of Lidding Foil
Embossing Station:
The Embossing Station Is Used For The Batch Number / Manufacturing And Expiry Coding On The Blister Pack.
The Station Is Pneumatically Operated. The Embossing Station Is Hot And The Temperature Is Controlled By Thermostat. Normally The Temperature Is Set At 110 Degrees.
The following Change Parts Are Required For Embossing:
- Anvil Plate
- Hammer Plate
- Embossing Guide Track
- The Code Types To Be Embossed Are Fitted In An Anvil Plate. The Anvil Plate Is Mounted On The Heater Of the Station. The Hammer Plate Is Mounted On The Opposite Side Of The Anvil Plate.
- The Station Has To Be Set In Position Depending On The Change Part. To Set The Vertical Position The Station Can Be Lifted Upward Or Downward On The Slotted Bracket Mounted On The Machine Front Plate.
- For Horizontal settings, The Embossing Guide Track Is Provided.
- The Embossing Operation Will Be ‘on’ Only When The Embossing ‘on-off’ Is Selected To ‘on’ And The Machine Is Running In ‘Run’ Mode.
- The Embossing Station ‘on-off’ Is Controlled By The Cam Switch Located At The Back Of The Machine. In The Cam Switch Box Assembly Driven From the Main Drive Of the Machine.
- The Embossing Type Holder Anvil Plate Can Be Easily Removed For Easy Changeover.
Critical:
- Temperature Of The Embossing Heater.
- Parallelity Of The Station.
- Perfect Straightening Of The Toggle Lever In Station ‘on’ Condition
Indexing Assembly:
This Assembly Is Mounted Before The Punching Station.
The Index Ratchet Is Used To Index The Blister Formed/filled And Sealed Web Through The Machine.
The index Is Driven By The Main Drive And Is of Intermittent Type.
It Consists Of The Following Parts:
- Indexing Ratchet (change Part)
- Advance Setter Slide
- Stroke End Setter Rod With Pusher
- Depending Upon The Pack Advance The Advance Setter Slide Can Be Adjusted.
- Perforation Station (optional)
- The Perforation Station Is Used For Inline Perforation And Cross Perforation.
- The Station Is Mechanically Operated And Driven From The Main Drive. The Drive Punching And Perforation Drive Sprocket Is Fitted With a Bone Fix.
- The Drive Is Transferred To the Connecting Crank At The Front, Which Is Attached To the Perforation Tool With The Help Of the Gudgeon Pin Holder.
- The Station Has To Be Set In Position Depending On The Change Part. This Is Done Through A Perforation Register Roller.
- The Perforation Tool Is A Change Part And Is Layout Specific. The Entire Tool Is Integral And Can Be Mounted Easily Onto The Perforation Station.
- The Perforation Blades Are Mounted On The Right-hand Side Movable Plate And The Die is on the Left-hand Side
- Fixed Plate.
Critical:
- Parallelity Of The Blades
- If The Blades Have Worn Or Are Damaged During Operation It Is Recommended To Immediately Replace The Blades. Or Else The Quality Of Perforation Will Be Poor.
Punching Station:
- The Punching Station Is Used To Punch The Pack From The Web.
- The Operation Is Mechanical.
- The Punching Tool (part Of the Change Part) Is Mounted On The Punching Station.
- It Can Be Easily Mounted On To The Machine.
- The Punching Station Is Driven By The Same Drive, that drives The Perforation Station.
- The Movable Part Of the Punching Tool, Which Contains The Punch Plate, Is Connected To the Connecting Crank For the Drive.
- The Fixed Part Of the Punching Tool (die Punch) Is Fitted On The Punching Station.
Critical:
- Burr Observed On-Pack – Punching Tool Worn Out, Requires Regrinding.
- Improper Punching – Timing Disturbed – Set The Punch Timing Concerning The Indexing.
Pack Pick And Place Assembly:
- This Mechanism Is Used For Rejecting Empty, Misfiled Blisters In The Rejection Chute And Placing The Good Pack On The Delivery Conveyor For Further Handling. (optional)
- It Consists Of A Suction Arm With Suction Cups, Which Picks Up The Pack From Punching Station After Punching And Releasing The Rejected Packs In The Rejection Chute.
- The Good Packs Picked Up By The Suction Arm Are Released At the Pack Delivery Conveyor.
- The Number Of Suction Arms depends upon The Number Of Packs Punched Out In One Punching Stroke.
- Pick And Place Operation Is Pneumatic And The Operation Command For The Pack Pick Up And Release Of Packs Is Given By The Programmable Logic Controller (plc).
- Vacuum Required For Pick Up Of Packs From Punching Is Generated By Vacuum Venturi And Is Connected To The Pick And Place Solenoid Valve.
Critical:
- Air Inlet Pressure For the Vacuum Venturi Should Be 1 ~ 2 Bar. If This Is Too Much Then Packs Will Not Be Released Properly And If This Is Too Low Then The Packs Will Not Be Picked Up Properly.
- Air Pressure For To Pack Release Solenoid Should Be Around 4 ~ 5 Bar.
Delivery Conveyor:
- The Delivery Conveyor Is Used To Transport The Punched Packs For Further Handling.
- The Delivery Conveyor, Is Driven By Ac Motor.
- The Speed Of The Conveyor Belt Can Be Regulated By The Invertor Plated In the Panel Of The Machine
Control Panel:
- The Control Panel Is Housed On The Right Side Of The Machine.
Control And Power Systems Are Accessed From The Rear Side, By Opening The Cover. - The Panel Houses
- The Transformer, Contactors, Miniature Circuit Breakers, Programmable Logic Controller (plc) Mitsubishi Fx On 64mt – Dss, Input Expansion Unit Mitsubishi 8ex, Relays, Timer, 5vdc Power Supply Card, 24vdc Power Supply Card And The Vibrator Drive Card.
The Swell Panel Consists Of: – - Operator Panel Mmi Touch Screen E615.
- Temperature Controllers For The Pre-heating Roller And Pressure Sealing Roller.
- Machine Start Push Button.
- Machine Stop Push Button.
- Emergency Stop Push Button.
- 3-Way Selector Switch For Jog Mode /set Mode And Run Mode.
- 2-Way Selector Switch For Embossing On-off.
- Potentiometer For Machine Speed Variation.
- Potentiometer For Vibrator Speed Variation.
- Potentiometer For Feeder Motor
- The Inverters Are Mounted Inside The Machine.
- The Control Circuit For The Machine Is 230 Vac.
- The Power Supply is To Be Connected To The Control Panel Via The Mains Socket Mounted At The Bottom Of the Left Hand Side Machine Frame Is 440vac 3 Phase + Neutral + Earth.
- The average Power Consumption By The Machine Is 4.5kw.
General Features for Design Qualification (DQ) blister machine:
- The Safety Guards Are Provided On The Machine With Safety Interlocks. All Movable Parts Are Guarded (optional).
- The Front and rear Doors Are Manufactured In Polycarbonate.
- All Mechanical Parts Are Treated With A Special Satin Chrome Plating. All Aluminium Parts Are Self-anodized. The Machine Is Ss Cladding.
- All Contact Parts Are Manufactured In Ss –316l Or Coated Depending Upon The Requirement.
Additional Base Material Reel Holder:
- The Additional Base Material Reel Is Loaded On This Unit.
- It Is Used To Support The Base Material When the First Reel Is Consumed. This Saves Loading Time During Operation.
- Loading Has To Be Done Manually On To The Shaft.
- Centering Of The Reel Is Done Manually By Adjusting The Cone On Both Sides Of Shaft.
- For Centering The Base Material Formula Applicable Is (a/2+151). Here “a” Is The Width Of The Base Material And 151 Is The Machine Center.
8.0 Technical Specifications Of Components & Sub-Components Used / Bought Outs
- S.no Details Of Equipment Make Number Rating Optional If Any.
- Plc Mitsubishi Fx0n-24mt-DSS
- MMI Biejer E615
- Invertor / Variable Speed Drive Mitsubishi 230v Ac/1 Hp
- Gear Box With A.C. Motor Bonfiglioli 230v(delta)/440v(star)/ 1 Hp
- Vacuum Pump Instavac 150 Lpm
- Vacuum Pump (motor) Siemens 0.37 kW
- Tablet Feeder Motor Remi Motor 1 / 20 Hp
- Vibrator Vibromex Vme- 230 V Ac
- Temperature Controller (film
- Heater) Fuji 24 Vdc
- Temperature Controller (sealing
- Heater) Fuji 24 Vdc
- Transformer (step Down) Powerpack —-400 Vac(p-440v, S1 -230v, S2 -24v)
- Potentiometer (for Ac Motor) Multi-turn Bourns —- 10 K Ohm 1 Watt
- Potentiometer (for Vibrator) Potel —- 50 K Ohm 3 Watt
- Regulator (for Feeder Motor) Rider —- 600 W 230 Vac
- Solenoid Valve For Power Cylinder
- Mfh 5 – 1/8 —-
- A For Film Contact Heater Festo —- 230 Vac
- B For Sealing Heater Festo —- 230 Vac
- Double Acting Power Cylinders —-
- 15 A For Film Contact Heater Festo 11252 Dgs-25-25ppv
- B For Sealing Heater Festo 14155 Dnu-63-40ppv
Others
1 Contact Heater Type
Plain Teflon Coated
2 Punching Station Standard
Pillar Type
3 Pressure Sealing Roller Standard
Srn-1
Certified That All The Above Parts Are Working Satisfactorily And The Machine Is Finally Ready For
Packing And Despatch.
9.0 Details Of Utilities
Sr. No.
Utility Description
Value In Dq
Method Of Verification
- Compressed Air Connection PU 6
Tubing @ 6 bar
Physical Verification
2 Electrical Supply 3 Phase
440V AC,
50 HZ,
Physical Verification
3 Cooling Water 120 Lt./hr. at 15 – 20°C Physical Verification
10.0 IDENTIFICATION OF COMPONENTS FOR CALIBRATION
ITEM S.NO.
Pressure Gauge _
Vacuum Gauge _
Temprature Controller (phr) _
Temprature Controller (phr) _
Temprature Controller (chiller) N A _
Vfd _
11.0 Material Of Construction
S.NO COMPONENT DESCRIPTION MOC
- Main Frame SS 304
- Hopper SS 316 L-2 mm
- Hopper Lid SS 316 L-2 mm
- Bowl Dish SS 316 L-2 mm
- Control Panel SS 304-2 mm
- Infeed Rubber Roller Silicon Food Grade
- Front plate Aluminium
- Guard polycarbonate
12.0 P&ID DIAGRAM FOR REFERENCE & APPROVAL
S.No Code No. Part Description Festo Part No.
1 A Compressed Air Supply Inlet. (PU – 6 Tube) 9159
2 B Air Filter Regulator Cum Lubricator
(FRC – ¼ – D – Mini) 159605
3 C Solenoid Valve MFH 3-1/8 7802
4 D Solenoid Valve MFH 5-1/8 9982
5 E Air Pressure Regulator with Gauge
(LR – ¼ – D – Mini) 159625
6 F Flow Control Valve GRL – 1/8 5668
7 G Double Acting Cylinder DSEU 40/25 – PA
(For Edge to Edge PRC) 188593
8 H Double Acting Cylinder ADV 32-25
(For Embossing) 9703
9 I Double Acting Cylinder DGS 25 / 25 PPV
(For Film Heater) 11252
10 J Double Acting Cylinder DNU 63/40 PPV – A
(For Sealing Heater) 14155
11 K Solenoid Coil MSFG 24VDC
(MFSG – 24 / 42 – 50/ 60) 4527
12 L Vacuum Generator VAD ¼ 9394
13 M Solenoid Valve MFH 3-1/8 SEU. 11121
14 N Lever for Pick and Place —-
15 O Pal Manifold 1/8 – 6 9767
16 P Pal Manifold 1/8 – 4 8603
17 SP1 Air Pressure Switch (Indofos) IPS – 100 —-
18 FCV1 Flow Control Valve GRL – ¼ 5666
Approval status: APPROVED/ NOT APPROVED
Any change in the approved diagram: Yes/ No.
If yes, the reason for the change
…………………………………………………………………………………………………………………………………………………………
…………………………………………………………………………………………………………………………………………………………
……………………
13.0 EQUIPMENT ORIENTATION WITH ROOM LAYOUT:
Attached as annexure-………
Approval status: APPROVED/ NOT APPROVED
Any change in the approved orientation layout: Yes/ No.
If yes, the reason for the change
…………………………………………………………………………………………………………………………………………………………
…………………………………………………………………………………………………………………………………………………………
…………………………………………………………………………………………………………………………………………………………
14.0 SAFETY FEATURES AND ALARMS:
The Design Qualification (DQ) blister machine is equipped with the following safety feature
- The emergency switch-one switch is provided on the swivel panel and other on guards
- The front guard and back door switch
- Pvc micro switch on material
15.0 FAT PROCEDURE for Design Qualification (DQ) blister machine:
Factory Acceptance Test Procedure shall be as follows:
After the completion of the erection work of the machine, the client shall be informed to perform the factory
acceptance test (FAT).
The client shall perform the FAT at the manufacturer site and record all the data in the prescribed FAT document
as per the details given below:
- Test criteria
- Design Verification Checklist
- Deficiency & Corrective Action Report
- Pre-installation requirements
- Final report
16.0 CHANGE CONTROL PROCEDURE:
Change in the agreed design shall be addressed through the Well-defined Change control procedure
17.0 Design Qualification (DQ) blister machine REPORT APPROVAL
17.1 Summary:
17.2 Certification:
1.0 APPENDIX
18.0 REFERENCE DOCUMENTS
- Manufactures Brochure (s) / Manual (s). (Title and Location) To be supplied with the Installation qualification documents
- Instruction and maintenance manual, Refer user’s manual
- Purchase Order Attached (Yes / No). If no, state the Location.
Yes– Attached (P.O. No. , dated ____) with DQ Document