1.0 Objective: The objective of this procedure is to provide guidelines for the operation of a Fluid Bed Dryer.
2.0 Scope: This procedure applies to the operation of the Fluid Bed Dryer located in the manufacturing area.
3.0 Responsibility: The Operator, Officer, and Executive of the Production Department, as well as the Manager of the Production Department, are responsible for following this procedure.
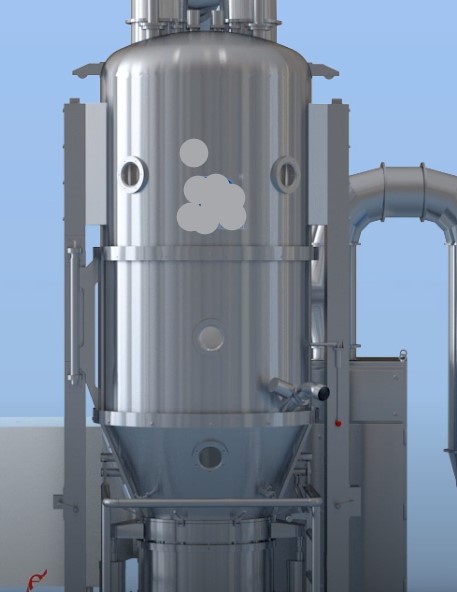
4.0 DEFINITION(S):
NA
5.0 Procedure:
5.1 Machine Setting:
5.1.1 Ensure that the equipment has a “CLEANED” label, duly filled and signed. Verify the cleanliness of the area and equipment. Record the observations in the equipment usage log sheet following SOP No. PRD/006-00. Affix an “UNDER PROCESS” label, duly filled and signed, on the equipment.
5.1.2 Unlock the control panel and turn the main switch to the “MAINTAIN” or “AUTO” position. The main air pressure gauge reading will start increasing, and the opening screen will appear on the Man Machine Interface (MMI). Ensure that the compressed air pressure is between 5.5 to 6 bar.
5.1.3 Tap “MAIN MENU” on the MMI. The main menu screen will appear. Tap “LOGIN” on the MMI. The keypad will appear. Enter the correct password and tap “ENTER” for confirmation.
5.1.4 Tap “MANUAL” on the MMI. The manual mode main screen will appear.
5.1.5 Tap “FBG LIFT LOWR” on the MMI. The pneumatic cylinder will come down.
5.1.6 Attach the FBT supporting ring to the fringes of the finger bag and tighten the rope.
5.1.7 Fix each finger of the finger bag one by one on the respective hook of the finger bag hanger.
5.1.8 Clamp the finger bag hanger onto the pneumatic cylinder.
5.1.9 Attach the compressed air supply pipes to the FBT supporting ring.
5.1.10 Tap “FBG LIFT LOWR” on the MMI. The pneumatic cylinder will start lifting up. Guide the guide rollers manually into the track.
5.1.11 Place the FBD bowl containing the material to be dried between the lower plenum and retarding chamber and lock the clamps. Insert the product bed temperature sensor into the temperature sensor port of the product container.
5.1.12 Tap “PC SEAL VENT” on the MMI. The pressure reading on the PC pressure gauge should increase to 2.5 to 3 bar.
5.1.13 Tap “FBD SEAL VENT” on the MMI. The pressure reading on the FBT pressure gauge should increase to 2.5 to 3 bars.
5.1.14 Tap “MAIN MENU” on the screen. The main menu screen will appear.
Note: Turn OFF the main compressed air while hanging the FBD finger bag or whenever the pneumatic cylinder is lifted lower.
5.2 Recipe Edit / Load / Delete:
5.2.1 Recipes can be edited, loaded, or deleted in both auto and manual modes.
5.2.2 Tap “RECIPE” on the MMI. The recipe main screen will appear.
5.2.3 Tap “EDIT” on the MMI. The recipe edit main screen will open with the following menu: Program No., Product Name, Batch No., Lot No., Operator Code, FBD Tag No., Product Code, Batch size, Manufacturing Date, Expiry Date.
5.2.4 Load the Product Name, Batch No., Lot No., FBD Tag No., Product Code, Batch size, Manufacturing Date, Expiry Date as per the respective Batch Manufacturing Record (BMR).
5.2.5 Tap “NEXT” on the MMI. The “RECIPE EDIT-1” screen will open with the following menu: Process Time, Air Dry Time, Spray Time, Spray OFF Time, Spray ON Time, Shaking Interval, Shaking Duration, Piston Up, Piston Down, Cooling Time, End Shaking Time, Piston Up, Piston Down.
5.2.6 Load the Process Time, Air Dry Time, Shaking Interval, Shaking Duration, and Cooling Time as per the respective BMR.
5.2.7 Tap “NEXT” on the MMI. The “RECIPE EDIT-1” screen will open with the following menu: Inlet Temperature, Outlet Temperature, Inlet High, Spray Temperature, RH Set Point, Print Interval, DP across HEPA Set, DP across FBT Set, Spray Pump speed.
5.2.8 Load the inlet temperature, outlet temperature, inlet high temperature, RH set point, print interval, DP across HEPA, and DP across the finger bag.
5.2.9 Tap “LOAD” on the MMI. The recipe load screen will open and display the details of the loaded process parameters.
5.2.10 Tap “STORE” on the MMI. The keypad will open. Enter a suitable name or code for the recipe. The recipe will be loaded in the PLC memory under the given name or code.
5.2.11 Tap “MAIN SCREEN” on the MMI. The recipe main screen will open.
5.2.11.1 To load an already existing recipe, tap “LOAD” on the MMI. The stored recipe list will open. Select the recipe and tap “ESC” on the MMI. A warning “LOAD RECIPE XYZ” (XYZ indicates the name or code for a particular recipe) will appear. Tap “YES” to load the selected recipe.
5.2.11.2 To delete an already existing recipe, tap “DELETE” on the MMI. The stored recipe list will open. Select the recipe and tap “ESC” on the MMI. A warning “DELETE RECIPE XYZ” (XYZ indicates the name or code for a particular recipe) will appear. Tap “YES” to delete the selected recipe.
5.3 Manual Mode Operation:
5.3.1 Ensure the main switch on the control panel is in the “MAINTAIN” position.
5.3.2 Tap “LOGIN” and enter the password.
5.3.3 After completing the machine setting, tap “MANUAL” on the screen. The manual mode main screen will open.
5.3.4 Tap “MAN-1” on the MMI. The Man-1 screen will open.
5.3.5 Tap “BLOWER” on the MMI. The blower will start.
5.3.6 Tap “BYPASS DAMPER” on the MMI. The Bypass Damper screen will open. The current status of the inlet air temperature, outlet air temperature, product bed temperature, air velocity, DP across HEPA, and finger bag will also be displayed on this screen. Set the bypass damper ON/OFF % depending on the inlet air, outlet air, and product bed temperature. Tap “BYPASS DAMPER” on the MMI to turn the bypass damper ON/OFF.
5.3.7 Tap “PRV” to return to the previous screen.
5.3.8 At the end of the operation, tap “BLOWER” on the MMI. The blower will stop.
5.3.9 Tap “MAN” on the MMI. The manual mode main screen will open.
5.4 Auto Mode Operation:
5.4.1 Ensure the main switch on the control panel is in the “AUTO” position.
5.4.2 Tap “LOGIN” and enter the password.
5.4.3 Tap “AUTO” on the MMI. The auto-selected screen will open, displaying the inlet, outlet, and product bed temperatures.
5.4.4 Tap “START” to start the process on the MMI.
5.4.5 Tap “HOT WATER” on the MMI. The hot water setting screen will open. Set the hot water ON and OFF times.
5.4.6 Tap “PREV” on the MMI. The auto-selected screen will open.
5.4.7 Tap “IND” on the MMI. The next screen will open, displaying the current process status (e.g., “Air Dry Time Started”). The set and actual values for the inlet, outlet, and product bed temperatures, DP across HEPA and finger bag, and air velocity will also be displayed on the screen.
5.4.8 Tap “IND 2” on the MMI. The screen will show the set and actual relative humidity (RH), % of FC damper opening, and % opening of the bypass damper.
5.4.9 Tap “MAN” on the MMI. The auto-selected main screen will open.
5.4.10 The process will run as per the set parameters and stop automatically upon completion of the cycle.
5.4.11 Tap “MAIN SCREEN” on the MMI. The main screen will open. Tap “LOGOUT” on the MMI. The message “OK, you are Logged Out” will be displayed on the MMI.
Related SOP: SOP on Operation of Rapid Mixer Granulator
5.5 Product Unloading:
5.5.1 Open the Manual mode main screen.
5.5.2 Tap “PC SEAL VENT” on the MMI. The pressure reading on the PC pressure gauge will decrease to 0 bar.
5.5.3 Tap “FBD SEAL VENT” on the MMI. The pressure reading on the FBT pressure gauge will decrease to 0 bar.
5.5.4 Tap “MAIN MENU” on the screen. The main menu screen will appear.
5.5.5 Tap “OPENING SCREEN” on the MMI. The opening screen will open.
5.5.6 Remove the product bed temperature sensor.
5.5.7 Open the clamps and remove the product container.
5.5.8 Tap “FBG LIFT LOWR” on the MMI. The pneumatic cylinder will come down.
5.5.9 Remove each finger of the finger bag from the hooks of the finger bag hanger.
5.5.10 Remove the compressed air supply pipes from the FBT supporting ring.
5.5.11 Untighten the rope around the FBT supporting ring and take out the finger bag.
5.5.12 Turn the main switch to the “OFF” position. The MMI will turn off, and the reading on the main air pressure gauge will reduce to 0 bar. Lock the control panel.
5.6 Affix a “TO BE CLEANED” label duly filled and signed on the FBD and record the observations in the equipment usage log sheet as per the given SOP.
Abbreviations:
BMR: Batch Manufacturing Record
FBD: Fluidized Bed Dryer
MMI: Man-Machine Interface
SOP: Standard Operating Procedure
HEPA: High-efficiency particulate air
PC: Product Container
DP: Differential Pressure