Housekeeping plays a significant role in pharmaceutical cleaning and especially disinfectant the critical area where direct manufacturing of medicine takes place, But before the audit, a housekeeping supervisor must be aware of below following Housekeeping Audit checklist points to successfully face at the end.
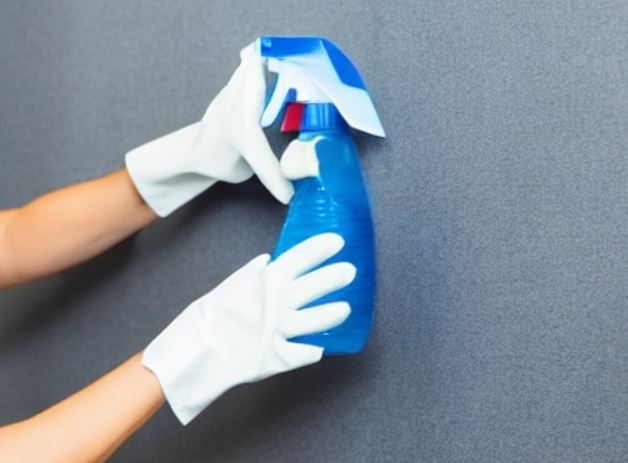
Related: SOP for Cleaning and operation of Vacuum cleaner
List of Housekeeping Audit checklist
- Computer terminals are free from post-it notes.
- Documents are located in respective areas.
- No stray documents online.
- All furniture/cross-over benches are clean & tidy.
- The floor was found properly swept and kept clean.
- Waste bins are in properly marked areas and used for applicable materials only.
- Area waste bins are not overflowing.
- Fire extinguishers and hoses are visible and accessible.
- All fire extinguishers hold their validity.
- All fire/emergency exits are unrestricted.
- All containers clearly identified.
- All materials are clearly labeled at their respective places.
- All equipment and tools not in use are stored in designated areas
- Cleaning & Sanitizing/disinfectant agents are appropriately identified & controlled.
- Lighting fixture, fan, switchboard, etc., clean.
- Tables, Chairs, Racks, Cupboards, etc., clean.
- Roof & wall free from dust/cobwebs.
- Floors are free from waste & spills.
- Stairs/staircases swept properly and approach clear.
- Window glasses, light glasses, and partition glasses are clean.
- Gangways/passages clearly marked and free of materials.
- Drains kept clean and unobstructed.
- Machines and equipment were kept clean and guards were in place.
- Machines and equipment free from accumulation of oil, grease, etc.
- Materials (RM/PM/semi-finished/Finished) are stored on pallets in their identified areas.
- Shop floor clear from scrap and other unwanted materials.
- Materials are stacked, identified, and stored in an orderly manner.
- Check if any Wastage/Leakage of water, fuel, electricity, steam and compressed air.
- Ventilation and mesh are proper and clean.
- Free from loose or hanging temporary wiring or Earthing broken.
- Equipment Status boards, in position and up-to-date.
- Lavatory blocks are clean & deodorized
- Free from Water spillage.
- Lockers are kept clean and in an orderly manner.
- First aid boxes available at proper places.
- Ensure that Exhausts and dust collectors are cleaned & properly working.
- Disposal of garbage is done regularly / frequently as necessary.
- Workers with necessary uniform.