1.0 Objective: 1.1 To describe the procedure for the Action Plan of Deviation
2.0 Scope 2.1: This procedure applies to the Purchase department in pharmaceuticals
3.0 Responsibility: 3.1 Asst. Manager- Purchase
4.0 Accountability: 4.1 General Manager – Purchase in coordination with respective Department Heads like QC and Stores.
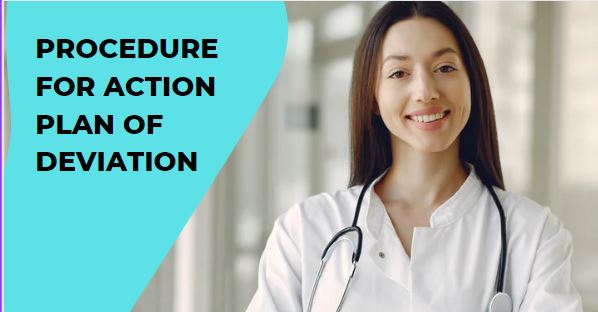
5.0 Procedure For Action Plan of Deviation
5.1 The nature of deviations may be as follows:
5.1.1 Deviation in Documents, Physical Quantity – Shortages, weight, Damage to the Contents and materials, processes, and Wrong Deliveries.
5.2 Deviations in Documents:
5.2.1 Arrange for corrections in documents for typographical mistakes observed at the time of material receipt.
5.2.2 Arrange when documents like Certificate of Analysis are not available along with the consignment
5.2.3 Send back when the Original Bills are not prepared as per the terms and conditions of the Purchase Order, and get corrected Bills.
5.3 Deviations in Physical Quantity – Shortages.
5.3.1 Confirm the shortages by comparing Material Receiving Report, Deviation Report Received from the Factory, and Acknowledgment submitted by the Approved vendor.
5.3.2 If the Approved Vendors supply the shortages within the stipulated time agreed in the Purchase Order, confirm the full quantity or else arrange payments proportionately.
5.4 Deviations in Weight
5.4.1 Confirm the Quantity by comparing Material Receiving Report, Deviation Report Received from the Factory, and Acknowledgment submitted by the Approved vendor.
5.4.2 If the Approved Vendor supplies the Balance Quantity within the stipulated time agreed in the Purchase Order, confirm the full quantity or else arrange payments proportionately.
5.5 Deviations as Damage to the Containers and Materials
5.5.1 If the damage is observed to only containers instruct the vendor to take appropriate actions not to repeat it in future supplies.
5.5.2 If the material got damaged or contaminated confirm the partial quantity by comparing Material Receiving Report, Deviation Report, and acknowledgment.
5.5.3 If the Approved Vendor supplies the Balance Quantity within the stipulated time agreed in the Purchase Order, confirm the full quantity or else arrange payments proportionately.
Related: Travel Policy in Pharmaceuticals
5.6 Damaged may be observed in Processes
5.6.1 If any damage is observed in Processes QA and QC department investigates the problem.
5.6.2 Head – QA is authorized for material destruction/rejection.
5.6.3 Receive the copy of the Destruction Report and inform to Approved Vendor.
5.6.4 Approved vendors may visit the factory to confirm the deviation and destruction. In the case of Printed material, the destruction shall take place within the factory.
5.6.5 Other than Printed material vendor can make arrangements to take back the online rejections.
5.6.6 The amount involved in “online rejections” can be settled either in future supplies or in terms of excess supplies.
5.7 Wrong Deliveries
5.7.1 Wrong deliveries shall be sent back in the same vehicle to the vendor with a “Deviation Report.”
5.7.2 Confirm the Quantity by comparing the Material Receiving Report, Deviation Report Received from the Factory, and Acknowledgment submitted by the Approved vendor.
5.7.3 If the Approved Vendors supply the Balance Quantity within the stipulated time agreed in the Purchase Order, confirm the full quantity or else arrange payments proportionately.
Related: Induction Policy in Pharma
6.0 Abbreviations:
SOP: Standard operating procedure
QA: Quality assurance
QC: Quality control