1.0 Objective: To lay down the procedure for the Cleaning and Operation of leak test apparatus.
2.0 Scope: This procedure is applicable to the cleaning and operation of leak test apparatus which is used for the Leak test of filled bottles in the liquid department.
3.0 Responsibility: Operator, Officer – Production Department
Manager- Production Department
4.0 PROCEDURE
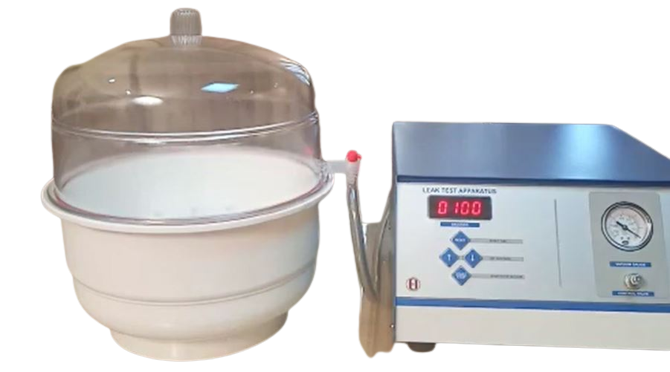
4.1 Cleaning
4.1.1 Carry out the following procedure after every test
4.1.2 Ensure the instrument is switched off.
4.1.3 Remove the vacuum connection to the desiccator.
4.1.4 Remove the clear top lid of the leak test apparatus.
4.1.5 Remove the bottles from the perforated disc and put them in the NRR container.
4.1.6 Remove the blotting paper from the perforated disc and carry out the moping with a lint-free cloth if there are any stains use a wet lint-free cloth.
4.1.7 Dry it with a cleaned dry cloth.
4.1.8 Fix the gasket and assemble the desiccators & lid and connect the vacuum connection.
4.1.9 Record the cleaning detail in Annexure- I (leak test apparatus cleaning record).
4.2 Set up and Operation
4.2.1 Vacuum and Time set up
4.2.2 Ensure the cleanliness of the leak test apparatus.
4.2.3 After line clearance from QA, put the “UNDER PROCESS” label dully filled and signed on the machine.
4.2.4 Switch on the main power supply of the instrument.
4.2.5 Switch the ‘ON’ of the instrument.
4.2.6 Set the vacuum up to 300 mm Hg.
4.2.7 After setting the vacuum, further set the hold time for 01 minute as per the following procedure:
- PRESS RESET ( wait till the scrolling display stops)
- TENS (Do not press this key)
- PRESS UNITS → Set time for 01 minute (VACCUM HOLD TIMER)
4.2.8 Checking the bottles for leakage
4.2.8.1 Collect the sealed bottles from each sealing head of the bottle sealing machine as per the frequency mentioned in the respective Batch Packing Record
4.2.8.2 Identify each head by putting a number on each sealed bottle with a marker.
4.2.8.3 Put blotting paper to cover the perforated disc of desiccators and Place each bottle in an inverted position on blotting paper.
4.2.8.4 Insert the lid on the bowl and close the red colored three ways key
4.2.8.5 Open three ways key and apply the vacuum by pressing the START key.
4.2.8.6 The vacuum pump will start and watch the vacuum building up on display
4.2.8.7 Once the “Set Vacuum” is reached, the pump will stop and the timer will start (Hold time).
4.2.8.8 When the timer comes to ‘Zero’, the vacuum releases automatically. Open the bowl remove the bottles one by one from the bowl and check the blotting paper for the presence of stains.
4.2.8.9 If no stains are observed on blotting paper, bottles leakproof, and sealing are satisfactory.
4.2.8.10 If leakage is observed from any one head rectify of particular head or heads. If leakage is not observed, continue filling.
4.2.8.11 Record the same in the respective BPR.
4.2.8.12 Leak test to be performed at the start of batch and after every two hours of the batch run alternatively by production and QA.
4.3 Precaution
4.3.1 Ensure that there is adequate lighting while carrying out the leak test.
Related: SOP For The Operation Of Multimill
5.0 Abbreviations:
SOP: Standard Operation Procedure
No. : Number
Q.A.: Quality Assurance
Annexure- I (leak test apparatus cleaning record)
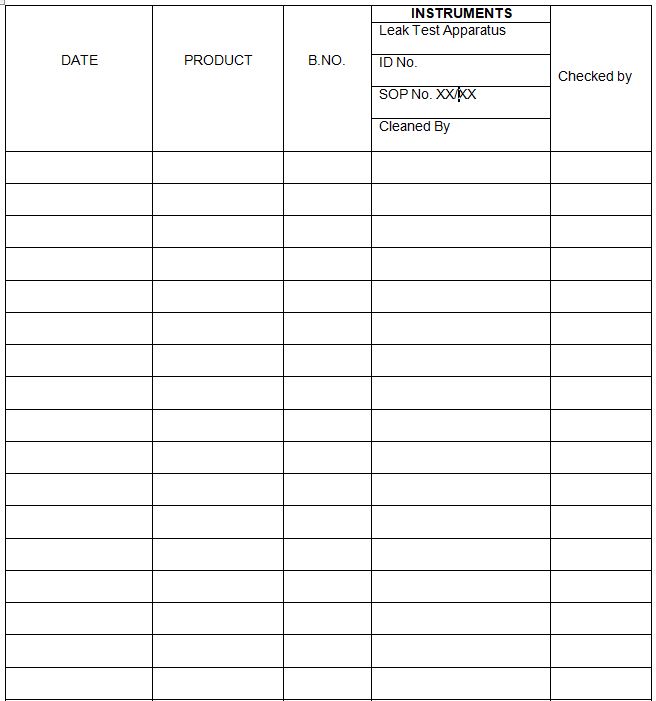