1.0 Objective: To establish a procedure for operating the strip pack machine.
2.0 Scope: This procedure is relevant to the operation of the strip pack machine within the production department.
3.0 Responsibility: Operators, Officers, and Executives in the Production Department hold the responsibility for this procedure. The Production Department Manager also has a role.
4.0 Definitions: None applicable.
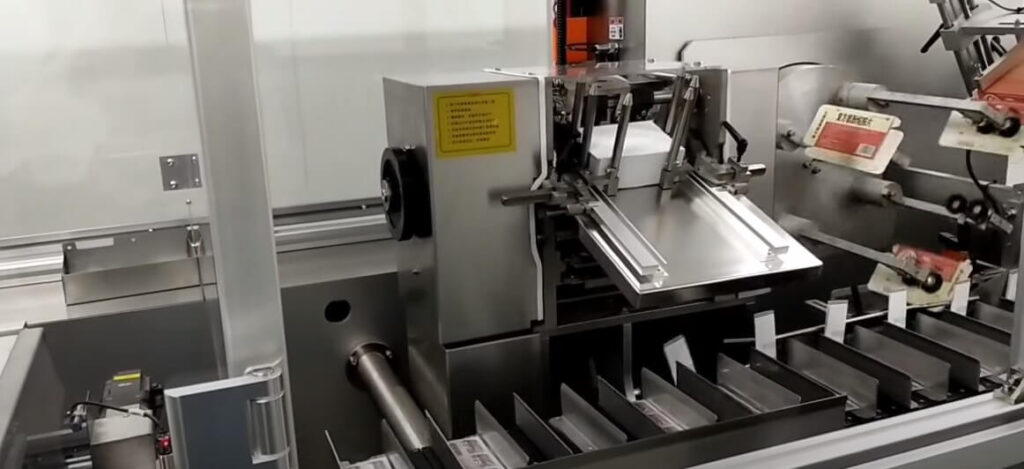
5.0 Procedure:
5.1 Machine Setting:
- Ensure that the main switch is in the “OFF” position.
- Mount the sealing roller onto the shaft and tighten the grub screw.
- Confirm that the centerline of the rollers aligns precisely above the centerline of the brush draw.
- Adjust the right sealing roller’s position using studs and nuts for parallel alignment.
5.2 Adjustment of Sealing Pressure:
- Check the alignment of the sealing rollers’ cavities.
- Tighten the pressure-setting stud to achieve proper sealing pressure until the packing material gets knurled.
- Gradually tighten the stud for pressure equalization until the packing leaves the sealing roller correctly positioned across the web.
5.3 Adjustment of Cutting Device:
- Verify the proper functioning of both cutting device cams.
- Push the cutter assembly downwards to activate the moving blade’s scissor action.
- Adjust the cutting assembly’s point by loosening screws and turning the hand wheel.
- Modify the cutting length using change gears and adjust screws on the cam disc.
5.4 Adjustment of Dropping Tablets:
- Adjust tablet dropping by loosening the socket head cap screw and adjusting the pin ring on the left-hand roller shaft.
- To delay or advance tablet dropping, rotate the back gear with the pin ring clockwise or counterclockwise accordingly.
5.5 Operation:
- After receiving line clearance from Quality Assurance (Q.A.), affix the “UNDER PROCESS” label on the machine.
- Record the batch’s operation time in the equipment usage log sheet.
- Turn on the main switch from the electrical panel.
- Inspect the strips with tablets and ensure:
- Proper knurling for smooth pressure.
- Tablets drop in the center of pockets to prevent cutting.
- Strips are cut to the required size in the knurling section to avoid cut pockets.
- Overprinting matches the Batch Packing Record (BPR). Check for ink smudging.
- Conduct the leak test as specified in the BPR.
- Manually set the sealing heater temperature using a screwdriver, in accordance with the BPR.
- Verify the temperature using a calibrated thermometer.
- Record the completion time of the batch in the equipment usage log sheet.
- Turn off the main switch from the electrical panel.
- Attach the “TO BE CLEANED” label to the machine at the batch’s end.
5.6 Precautions:
- Never operate the machine when empty.
- Clean the rollers using a soft brass wire brush.
6.0 Abbreviations:
BPR: Batch Packing Record.
Q.A.: Quality Assurance.
SOP: Standard Operating Procedure.
7.0 References:
SOP: Making entries in equipment usage and cleaning log sheet.
8.0 Annexures:
None available.