The main structure of the automatic vial sealing machine is protected by SS cabinet safety polycarbonate glass doors, and it also includes a Delrin slate conveyor, a screw that adjusts the height of the vials, a centralized lubrication system, an out-feed turntable, a vibrator bowl and chute for the cap, an in-feed screw, and star plate, sensors, an electrical panel, an AC Drive, a PLC, and an HMI. The Protocol for Performance Qualifications of a vial sealing machine involves the following stages:
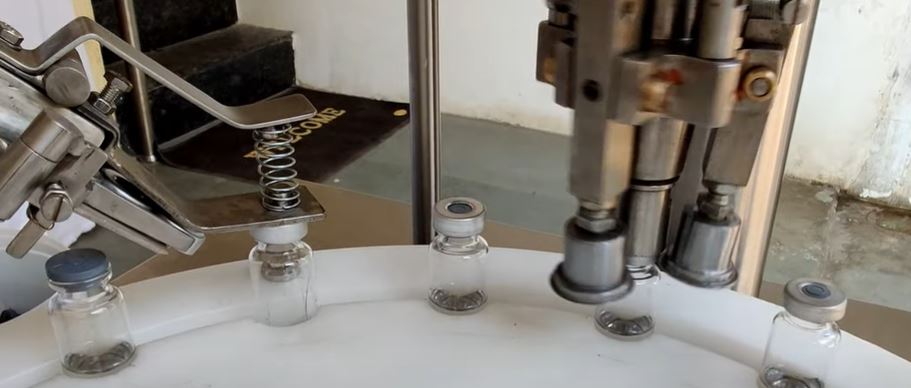
Instrument Name: Vial Sealing Machine
Location: Production
Protocol Content for Qualifications of vial sealing machine
S.No.
- Protocol Approval
- Overview:
- Objective Purpose and scope
- Responsibility
- Frequency
- Validation Team
- Acceptance Criteria
- Procedure
- System Description
- List of Reference SOPs
- Documentation
- Description of machine
- Experimental Details
- Filled Weight
- Overview
- Material Details
- Frequency of all parameters checking
- Noncompliance
- Validation Report
- Approval of Validation Report
OVERVIEW
2.1 Objective
The purpose of Performance Qualification is to confirm that the Vial Sealing Machine is capable of consistently performing as it is supposed to perform.
2.2 Purpose & Scope
To provide the documentary evidence that the Vial Sealing Machine is performing as per its intended use. The Vial Sealing Machine performance protocol applies to the Equipment Code Number. – XX -XXX.
2.3 Responsibility
Representatives from the following departments:
- Production: Preparation of Performance Qualification Record &Operation of Machine
- Validation: Verification & Compilation of PQ Record
- Quality Control: Sampling & Analysis
- Quality Assurance: Review & Control the Documents
2.4 Frequency :
The performance qualification should be done for the new facility.
Any major modification to any of the existing equipment after the validation activity must be documented through a change control system.
2.5 Validation Team:
- Representatives from :
- Production :
- Engineering :
- Quality Control :
- Quality Assurance :
3.0 ACCEPTANCE CRITERIA:
- Weight variation observed at all levels of the hopper and at all speeds should be between 98% to 102% of the standard limit.
- Nitrogen flushing should be achieved throughout the performance qualification.
- Rubber stoppering should be achieved properly.
4.0 PROCEDURE
4.1 SYSTEM DESCRIPTION:
Machine Name: VIAL SEALING MACHINE
Equipment Code No. : AC – 072
Manufacturer: Company Name
Customer: Company Name
Capacity: 100 Vials/min
4.2 LIST OF REFERENCE STANDARD OPERATING PROCEDURES:
- SOP for operation and cleaning of Vial Sealing Machine. SOP No: CO –
- SOP for operation and cleaning of Laminar airflow. SOP No: CO – 002
- SOP for environmental monitoring. SOP No: CF – 80
4.3 DOCUMENTATION:
- All documentation work shall be completed concurrently during the execution of the qualification. However, the protocol does not define the sequence of the test/ documentation to be carried out.
- Use indelible black ink for the recording.
- Fill out the complete information in the format provided.
- Do not leave any blank spaces.
- Correct the wrong entry by drawing a single line through incorrect data, recording the correct data, and then signing and dating the change.
- Enter “N/A” in a space that is not applicable.
- During the execution of the protocol, any deviation must be implemented as per the defined procedure.
- During protocol execution, the report shall be prepared with the following details.
- Discussion of all studies in the observation column.
- Qualification is completed or not.
- Conclusion.
- Recommendation, if any.
DESCRIPTION OF THE MACHINE:
- This is an automatic single-wheel Vial Sealing machine to Seal the vial containing powder products.
- This machine is an integrated machine with the following facilities/stations
- integrated suitably
- Infeed turn table
- Hopper for Aluminum Seal
- Turret
- Sealing station
- The machine is currently designed to operate with 7.5 &10 ml tubular vials
Vial carriage system/ process flow:
- The vials are fed to the in-feed rotary table from the conveyor belt of the tunnel and fed to the conveyor belt.
- The vial is then sensed by a sensor so that the Aluminum Seal drooped over the neck having a rubber stopper.
- Then the vials containing aluminum seal are sealed properly by the seal head.
- Then the vial is given out to outfeed the rotary table.
5.0 EXPERIMENTAL DETAILS:
Procedure:
- After completion of successful Operational Qualification check the performance of the powder filling line by filling anhydrous Lactose to ensure that the machine is performing as per its intended use.
- Ensure that the area and machine are cleaned before operation.
- Ensure that the LAF unit is cleaned and sanitized and that the LAF unit pressure is within the limit.
- Turn ON the electrical connection.
- Record the Sealing details in respective section tables.
- Check the sealing quality as per the frequency mentioned in the respective Table. Sealing quality will be only checked visually during the performance qualification run, the performance of sealing will be evaluated in terms of the successful media fill on the same line.
- The media fill report shall be an addendum to the qualification report.
- Check the sealing quality of vials and record the observations in the respective tables.
Note: In case of any deviation observed during Performance Qualification of the filling line with powder filling, inform to department head and quality head for necessary action.
- Document the deviation detail in the observed deviation section.
- The quality head and the department head will study the impact of deviation.
- If the deviation is acceptable and it does not have an impact on operation as well as on the performance of the machine, provide final conclusion.
- If the deviation is not acceptable, inform the quality head and department head for further action.
Read Also: Design Qualification (DQ) Blister machine
6.0 Validation Report:
The interim report shall consist of a summary document, in narrative form, which briefly describes the steps and observations during performance Qualification.
7.0 Approval of validation report:
The validation Executive shall evaluate the validation report before the Authorization of the General Manager of Quality Assurance and Quality Control (GM QA/QC) and General Manager Production. ( GM Production )