1.0 OBJECTIVE: To lay down a procedure for the cleaning of production areas in Pharmaceuticals.
2.0 SCOPE: The procedure is applicable to the cleaning of production area.
3.0 RESPONSIBILITY: Housekeeping personnel, Operator production, Officer, Executive – Production Department
Manager – Production Department
4.0 DEFINITION(S):
NA
5.0 PROCEDURE for Cleaning of Production area:
5.1 Ceiling/ AHU grill /dust collector pipe:
5.1.1 Frequency: Once a week or product change over which is earlier.
5.1.2 Climb on a ladder to clean the ceiling.
5.1.3 Wipe out the entire ceiling surface with a dry lint-free cloth followed by a wet cloth dipped in water. Wipe out again with a dry lint-free cloth.
5.1.4 Wipe the grill thoroughly from the outside with a wet lint-free cloth dipped in water, then wipe again with a dry lint-free cloth.
5.1.5 Wipe the outer side and inside of the dust collector pipe present inside the production area with a dry cloth to remove the adhered material.
Note: Dismantle the dust collector pipe, and the butterfly valve of the pipe and clean with purified water using a nylon scrubber during product changeover or the same product run for a week in the respective area.
5.1.6 Use safety goggles to prevent dust from falling into the eyes.
5.2 Walls / electrical fixtures /windows/doors:
5.2.1 Frequency: Once a week or product change over which is earlier.
5.2.2 Wipe the wall surface with a wet cloth dipped in water to remove all adhering material.
5.2.3 Wipe out the entire wall surface thoroughly with a dry lint-free cloth
5.2.4 Remove dust from panel frames, electrical switches, glass frames, and switchboards with a clean dry cloth.
5.2.5 Wipe the entire glass panels, windows, and doors with a cloth dipped in water.
5.2.6 Sprinkle a few drops of Colin (cleaning agent) over windows and doors. Wipe it out with a lint-free cloth.
5.2.7 Wipe the door closure thoroughly with a cloth to remove adhering material.
Note: Wipe all the tables with lint-free cloth dipped in purified water once a week
5.3 Floor:
Clean the floor with the help of a vacuum cleaner in the respective area.
5.3.1 Cleaned by scrubber machine:
5.3.1.1 Frequency: Twice in a shift.
5.3.1.2 Fill 10 ml of teepol into the scrubber machine and add a quantity sufficient to 10 liters of purified water in it and mix manually.
5.3.1.3 Clean the entire floor by using a scrubber machine.
5.3.1.4 Remove the above cleaning solution from the scrubber machine into the drainage of the washing area. Clean the scrubber machine.
5.3.1.5 Fill 20 liters of purified water in it and clean the entire floor by using a scrubber machine.
5.3.1.6 Fill 250 ml of Savlon / Dettol in the scrubber machine as per the enclosed area cleaning and sanitization checklist and add a quantity sufficient to 10 liters and disinfect the entire floor.
5.3.1.7 Drain the unused disinfectant solution from the scrubber machine into the drainage of the washing area.
5.3.1.8 Clean the scrubber machine as per SOP No.: PRD/049 and keep it in the washing area.
5.3.1.9 Note: Ensure that the pallets are moved aside so as to facilitate the
Proper cleaning of the floor beneath.
5.3.2 Manual cleaning and sanitization:
5.3.2.1 Frequency: Twice in a shift.
5.3.2.2 Take 10 ml of teepol in the SS bucket and add 10 liters of purified water and mix manually.
5.3.2.3 Dip a clean mopper in the above solution, squeeze, and then wipe out the floor thoroughly.
5.3.2.4 Drain the cleaning solution into the drainage of the washing area.
5.3.2.5 Take purified water in the SS bucket.
5.3.2.6 Dip a clean cloth in the purified water, and squeeze and wipe out the floor previously cleaned with a cleaning solution.
5.3.2.7 Drain the used purified water into the drainage.
5.3.2.8 Fill 250 ml of savlon / Dettol in SS bucket as per the enclosed area cleaning and sanitization checklist and add a quantity sufficient to 10 liters and disinfect the entire floor.
5.3.2.9 Dip a clean cloth in a solution prepared, squeeze, and wipe to disinfect the entire floor.
5.3.2.10 Repeat the procedure of dipping and squeezing the cloth in the disinfectant and wipe to clean the entire floor.
5.3.2.11 Drain the used disinfectant into the drainage of the washing area.
5.3.2.12 Clean the mopper with purified water and store it in the washing area dipped in a fresh disinfectant solution.
5.3.2.13 Clean the used buckets with purified water and keep them in the washing area in the inverted position.
Related: SOP for Operation and cleaning of Vernier Caliper
5.4 Precautions while Cleaning of Production area:
5.4.1 Use disinfectant savlon/Dettol on every alternate day.
5.4.2 Prepare the solutions of detergent and disinfectant at required concentrations in separate buckets.
5.4.3 Perform the cleaning operation in the direction from the far end of the department to the entry of the department to ensure complete dirt removal.
5.4.4 Use fresh solutions for cleaning each area.
5.4.5 Record the cleaning activity in the area as per Annexure –I and cleaning of the AHU grill and dust collector pipe as per Annexure–II.
6.0 ABBREVIATION(S):
ml: milliliter
SOP: Standard Operating Procedure
AHU: Air Handling Unit
SS: Stainless Steel
Annexure-I
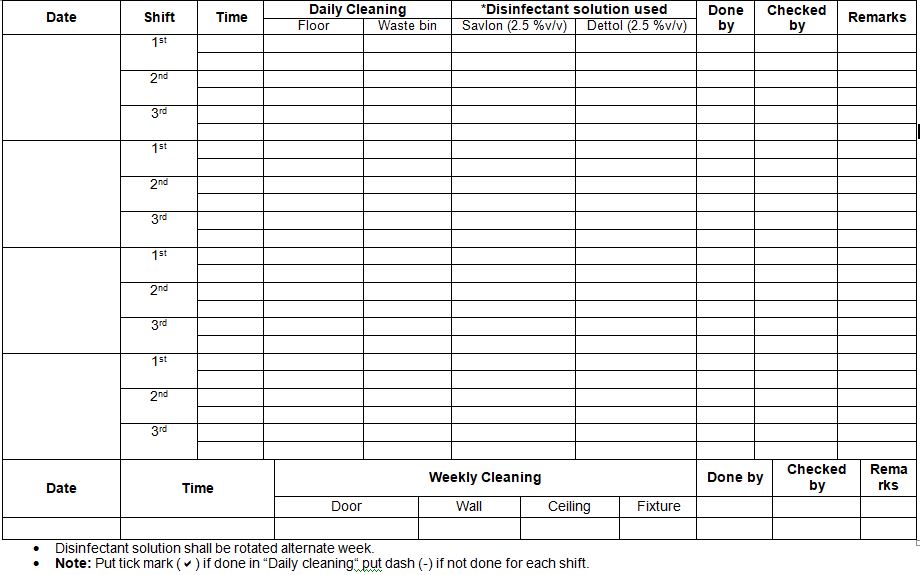
Annexure-II
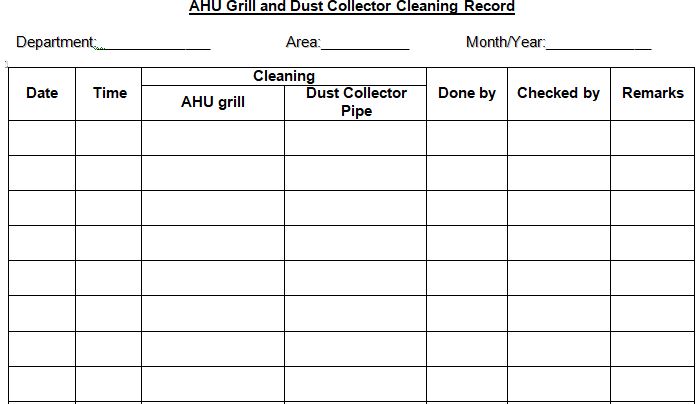