1.0 OBJECTIVE: The objective of this procedure is to define the process for the movement of materials from one stage to another within the production department.
2.0 SCOPE: This procedure applies to the movement of materials from one stage to another within the production department.
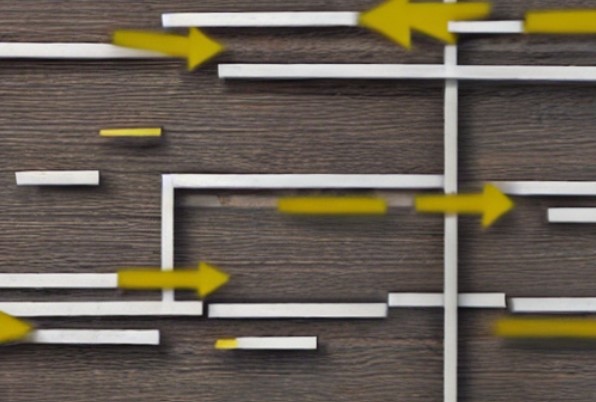
3.0 RESPONSIBILITY: The following personnel in the production department are responsible for implementing this procedure:
Operator
Officer
Executive
Production Manager
4.0 DEFINITION(S):
NA (Not Applicable)
5.0 PROCEDURE:
5.1 Store to Raw Material (RM) Hold:
5.1.1 Dispense individual materials using clean scoops. Transfer solvents from their containers to stainless steel containers.
5.1.2 Carefully transfer raw materials from intact containers to stainless steel containers or In-Process Containers (IPCs) lined with double polybags, using clean stainless steel scoops.
5.1.3 Use trolleys to transfer dispensed materials from the stores to the Raw Material (RM) hold area in the manufacturing section. Place them on stainless steel pallets.
5.2 RM Hold to Granulation Area for Sifting:
5.2.1 Crosscheck the weight of dispensed materials in the RM hold area.
5.2.2 Transfer dispensed materials from the RM hold area to the granulation area.
5.2.3 Manually transfer materials to the sifter using stainless steel scoops.
5.2.4 Collect sifted material in In-Process Containers (IPCs).
5.3 Sifter to Rapid Mixer Granulator (RMG):
5.3.1 Transfer sifted raw material to the RMG using a hoist.
5.3.2 Lift the IPC with sifted material and position it over the RMG charging window.
5.3.3 Load the material into the RMG by opening the valve of the In-Process Container.
5.4 Rapid Mixer Granulator to Fluidized Bed Dryer (FBD) for Drying:
5.4.1 Unload wet granules directly into the FBD bowl.
5.5 FBD to Sifter and Multimill for Sizing:
5.5.1 Transfer dried material from the FBD bowl to the sifter using a tipper. Pass the remaining material through the multimill.
5.5.2 Collect sized granules in IPCs.
5.6 Sized Granules for Lubrication:
5.6.1 Load sized material and sifted lubricants directly into IPCs.
5.6.2 Transfer blended materials to the granules stored in SS/HDPE containers with double-lined polybags.
5.7 Granulation Area to Granules Quarantine:
5.7.1 Transfer lubricated granules to the granules quarantine area in SS/HDPE containers with double-lined polybags.
Note: Granules can be kept in the quarantine area for up to 7 days before the next step.
5.8 Granule Quarantine to Compression:
5.8.1 Transfer material for compression from the granules hold to the compression cubicle in containers.
5.8.2 Manually feed lubricated granules to the hopper of the compression machine using scoops.
5.8.3 Collect compressed tablets below the de-duster in SS/HDPE containers lined with double polybags.
5.8.4 Transfer compressed tablet containers to the core tablet storage area (quarantined).
Note: Ensure that approved tablets are used for coating and packing.
Uncoated tablets can be kept in the quarantine area for up to 14 days before the next step.
5.9 Store to Coating:
5.9.1 Crosscheck the weight of dispensed material.
5.9.2 Transfer coating material from the store to the solution preparation area.
5.9.3 Transfer core tablets from the core tablet store to the coating area.
5.9.4 Transfer coating solution from the solution preparation room to the coating area.
5.9.5 Transfer coated tablets to the tablet storage area in SS/HDPE containers with double-lined polybags.
Note: Coated tablets can be kept in the quarantine area for up to 21 days before the next step.
5.10 Coating to Inspection Area:
5.10.1 Transfer coated tablets to the inspection area.
5.10.2 After inspection, transfer the tablets to the tablet quarantine.
5.11 Inspected Tablet Store to Blister/Strip Packing:
5.11.1 Transfer inspected tablets to the blister/strip/bulk packing area on pallets.
5.11.2 Transfer blister packs and strip packs on the conveyor belt to the packing area for packing into cartons.
Note: Never run more than two packing lines in the packing hall simultaneously.
5.12 Packing Area to Finished Goods Store:
5.12.1 Transfer packed goods to the finished goods store upon batch completion or at the end of the day, verified by the Quality Assurance department.
5.12.2 Dispatch packed goods to their respective locations as per requirements, after release from Quality Assurance.
5.13 Note: Make entries in the Inward/Outward register as per making entries in the inward/outward register SOP.
Related SOP: SOP on indenting Additional Packing Material
6.0 ABBREVIATION(S):
FBD: Fluidized Bed Dryer
HDPE: High-Density Polyethylene
IPC: In-Process Container
RMG: Rapid Mixer Granulator
RM: Raw Material
SS: Stainless Steel
7.0 REFERENCE(S):
NA (Not Applicable)
8.0 ANNEXURE(S):
Nil